PLC微机系统在联合站中的应用分析
在油田生产中,联合站原油生产过程是原油集输过程中的重要环节,联合站原油生产工艺的自动化控制水平直接影响外输原油的质量和油田的经济效益。油田开发早期,联合站采用的是常规仪表控制模式,随着计算机技术的发展,计算机控制技术不断应用在联合站的生产过程中。90年代初,萨北油田部分联合站应用的工控机控制技术,同常规仪表控制技术相比,它具有显示直观,控制稳定,故障率低等优点,但也存在风险集中,编程复杂,不宜增补控制参数,抗干扰性差、易死机等问题。
近年联合站、转油站集输系统开始尝试应用小型DCS 或PLC控制技术,该技术同以往控制技术相比具有明显的优越性。本文主要以PLC技术为代表,详细论述新型控制技术在联合站的应用情况。
2 控制原理
2.1 PLC 微机系统基本结构
PLC(Programable Logic Controller)即可编程逻辑控制器,最早是应用在数字逻辑处理的领域中,但随着应用范围和应用领域的逐步扩大,以及生产工艺的不断完善,现在的PLC系统在模拟量处理上取得了很大的进展,近年来已逐步地应用于工业自动控制中。
PLC系统分为下位机(现场控制站)和上位机(管理计算机)两级结构。通常由现场控制单元、过程接口单元、管理计算机以及信号联络线等几个部分组成,基本结构如图1。

图1 PLC 系统基本结构简要示意图
上位机:作为系统的人机接口,一般采用windowsNT4.0操作平台,应用CIMPLICITY组态软件,通过程序开发和系统的运行平台,完成数据显示、人机界面操作以及对整个工艺、自动化控制系统的管理、打印报表等。
下位机:PLC是整个系统的核心,PLC的各种模块可以根据需要,任意构成采集、控制单元,从而实现对测量、计量参数的采集和回路的控制,整个生产工艺过程的数据采集和过程控制都是由PLC来完成。
2.2 控制原理
下图为联合站过程控制原理示意图
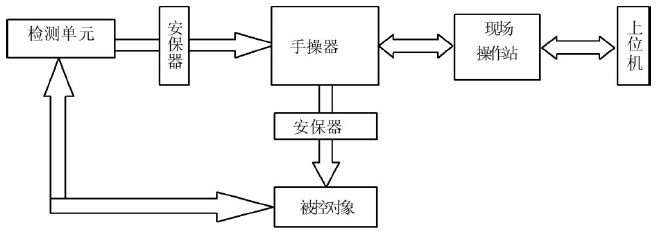
图2 控制原理方框示意图
现场一次表检测的液位、压力、界面、温度等输入信号,转换为电流信号后,输入到控制安保器,进行光电隔离,经手操作器进入现场控制站,CPU采集信号后,进行对比分析,通过PID调节,输出控制信号给执行机构,使调节阀动作,实现自动调节功能;现场控制站在故障情况下,可利用手操作进行手动操作,实现被控制对象平稳运行。
3 系统实现的功能
3.1 上位机实现的功能
3.1.1 窗口监视,包括总貌、组画面、点显示、报警、趋势、系统信息、历史记录等。
3.1.2 操作平台可设置报警参数及控制参数,并与实际参数对比,进行参数报警。
3.1.3 远程联络,可把现场数据传输给远程管理人员,对现场控制情况进行分析。
3.1.4可对现场控制参数进行自动与手动无扰动转换控制,达到出现故障时,手动调节能够及时的目的。
3.1.5 报表打印,可打印班报、日报、月报。
3.2 下位机实现的功能
3.2.1 现场数据的实时采集:测量变送单元将被控制参数进行测量转换成4-20mA直流信号,经光电隔离后,输入到控制器的I/O模块输出端输出,再输入到执行机构实现对控制对象的控制功能。
3.2.2对被控制对象实现过程控制:I/O模块输入端接受信号后,经数据运算处理后从I/O模块输出端输出,再输入到执行机构,实现对被控制对象的过程控制。
4 应用效果分析
目前,在联合站集输工艺控制系统中一般应用的有三种控制模式:一是常规仪表控制模式,二是单一的工控机控制模式,三是集散控制模式(或可编程控制模式)。
在常规仪表控制中,操作人员必须从仪表盘上逐台读取仪表的显示值才能了解生产运行情况,操作与监视相对困难,人-机联系差。在控制功能方面,由于一台常规模拟调节器功能单一,仅能实现一种控制功能,对于非线性、多变量控制等复杂功能,难以满足要求,而且采用仪表多,故障点位相对多,故障率高,相比之下,PLC系统具有显示直观,易于操作,故障率低的优点;在工控机控制中,工控机及其采用的A/D板,抗干扰能力相对较差,易死机,可靠性不高,而PLC系统由于整个生产工艺过程的数据采集和过程控制都是由PLC来完成,受到人为因素和环境因素的影响很小,故其系统可靠性高、抗干扰能力强,系统运行更稳定。
近年,在萨北油田的联合站、转油站及污水处理站、注聚站中,已逐步开始应用PLC微机系统控制技术,如:近年老改工程中在北部过渡带转油放水站、北二东区块联合站的改造中,自控系统全部更新为PLC微机系统;在转油中转站中萨北**站、北**等站也都应用了PLC微机系统,其它的象北**污水处理站、北**注聚配置站等也都已应用了PLC微机系统。下面就东部过渡带的北**转油放水站PLC微机系统控制技术的应用效果情况进行具体分析。
东部过渡带的北**转油放水站在前两年的转油放水站老改施工改造中,对原有的自控系统进行了全部更新,更新后北**转油放水站应用的是德国西门子公司生产的S7-300控制器(PLC)。从该站应用情况看,应用该系统不但实现自动控制投入少,控制稳定,自动化程度高,易于操作,而且可实现网络化管理,具体优越性表现在以下两方面:
4.1 增加了安全生产的可靠性
北**转油放水站共分为游离水、外输、沉降等3个生产岗位,由于每年的春季设备检维修检查、冬防保温检查等大型迎检检查,加上近年管理先进站上水平的工作量不断增加,岗位工人脱离值班室,在场区工作的时间也越来越长,无形中给安全生产带来了事故隐患。但在安装了PLC微机系统后,岗位的任何一员工,都可随时地、自如地通过微机监控到全站各岗的生产情况,从而消减了事故隐患的发生,增加了安全生产的可靠性。
4.2 大大提高了参数稳定性
在PLC自控系统更新前,北**转油放水站应用的是常规仪表控制模式,生产参数非常不平稳,运行曲线波动较大,时常有超出指标控制范围的时候;在PLC自控系统更新后,这种情况明显得到了改善,由于数据监控及时,人机界面操作简单方便,真正做到了“三勤五平稳”,生产参数运行曲线平滑,没有明显波动。
PLC微机系统控制技术的应用在显示其卓越的优越性同时,目前也存在以下两点问题:
(1)部分需进机参数还不全,如加热炉超高温报警系统无法使用、外输流量计累积量还不能显示等,需厂家尽快给予解决。
(2)系统出现问题,目前基本上都是厂家来人处理,岗位工人还不具备处理解决的能力,这方面还需要厂家对值班人员进行培训。
5 结语
5.1 PLC微机系统由于实现现场数据采集和过程控制,同单体表控制相比,故障率低,控制可靠,并可实现信息共享,提高自动化控制水平和系统可靠性;同工控机控制系统相比,抗干扰性强,控制稳定,风险降低,安全可靠,而且编程简单,易于修改和扩充。
5.2采用PLC微机系统,实现网络监测、管理、操作及报表打印功能,便于对生产运行状况进行监控和操作,大大减少岗位操作人员的劳动工作量。
5.3 根据萨北油田的应用情况,建议将PLC微机系统控制技术在全油田大面积推广。