溶气气浮分离乳化油的影响因素
在石油开采、炼制及化工生产过程中会产生含油废水,如处理不当进入环境水体,将对环境造成污染。对于直径较小或密度与水接近的油滴,传统的重力沉降难以达到令人满意的效果。气浮通过向污水中加入微气泡,与油滴粘附形成絮团,可提高油水分离效率。
专家学者应用溶气气浮对不同水体中的油进行了分离实验,主要关注气浮池结构、操作参数及油水种类等因素对浮选除油效果的影响,而极少关注各因素对除油效果的影响机理,缺乏相应的理论分析。所以本文在进行气浮除乳化油实验的同时测量气泡直径、气含率等参数并观察乳化油形态,分析溶气压力及化学助剂对除油效果的的影响机制,以期指导溶气气浮的工业应用。
1、实验部分
1.1 实验流程及装置
溶气法生成微气泡的装置主要包括溶气罐和释放头。实验时回流水泵和空气压缩机分别将水和空气注入高压溶气罐内,两相在溶气罐内混合,空气溶解形成饱和溶气水。饱和溶气水到达释放头后减压释放,气泡成核析出,形成大量微气泡。实验过程中可以通过调节回流水泵的流量改变溶气压力。
进行除油实验时,含乳化油污水经提升泵进入气浮池接触区,与微气泡混合。在此过程中,气泡与乳化油滴发生粘附形成絮团。絮团进入分离区后上浮至水面。处理后的净水由分离区底部孔道进入回流水收集区,部分作为溶气水源,部分进入污水处理池,形成循环流程。
1.2 含乳化油污水制备
为了对乳化油状态进行显微观察,首先取原油140g加入航空煤油至1L,配成带有颜色的污油。乳化时取50mL 污油加水至500mL,同时加入乳化剂十二烷基苯磺酸钠(SDBS,分析纯)2.5g,使用高速剪切乳化机进行乳化,制成高浓度含乳化油污水。实验时根据所需浓度加水进行稀释,制成一定含油浓度的污水。
1.3 气泡直径测量方法
本研究采用图像分析法测量气泡直径。首先使用数码显微镜(PH50型)拍摄气泡群的显微放大图像,后采用自编的Matlab程序对图像进行处理,得到气泡直径分布,具体测量及图像处理过程。
1.4 除油效率的测量
含油浓度的测量根据碎屑岩油藏注水水质推荐指标及分析方法(SY/T 5329)进行。测量前绘制含油浓度标准曲线,测量时取含油污水用石油醚(分析纯)进行萃取,利用分光光度计测量吸光度ABS并换算成水中含油浓度。
采用除油率表征乳化油分离效果,除油率η 计
算式如下:

式中,ρ0为浮选前污水含油浓度,ρ 为浮选后气浮出口处含油浓度。
2、结果与讨论
2.1 溶气压力的影响
溶气压力是气浮工艺中一个重要操作参数,首先采用不同溶气压力进行除油实验,分析其对除油率的影响。实验采用污水初始含油浓度为1000mg/L,溶气压力分别为0.22、0.26、0.30、0.34MPa。不同溶气压力下除油率随时间变化如图1 所示。由图1 可知,0至20min除油率变化最显著, 20min以后除油率增大速率减缓,60min后除油率基本不再发生改变。溶气压力由0.22MPa增大至0.26MPa时,最终除油率由30%左右升高至40%以上。而溶气压力在0.26MPa至0.34MPa变化时,最终除油率基本不再发生改变。在实际应用中,提高溶气压力伴随着能耗的增加,但分离效率不再增大,所以实际操作过程中溶气压力并非越大越好,需确定最合理的溶气压力。
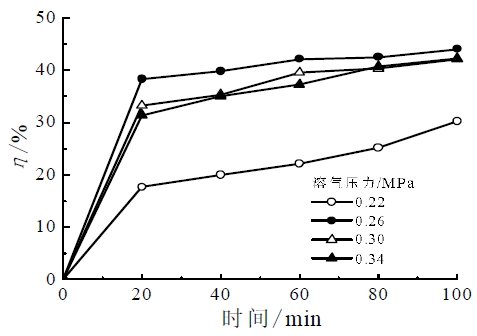
图1 压力对除油效率的影响
为分析溶气压力对除油效果的影响机制,对不同溶气压力下气泡(释放头处产生的气泡)直径及气含率进行了测量,结果如图2 所示。由图2 可知,溶气压力由0.22MPa升高至0.26MPa,生成的气泡直径由63.2μm减小至38μm,溶气压力继续增大至0.34MPa,气泡直径由38μm减小至30μm。回流水中的气含率随着溶气压力的升高而增大。
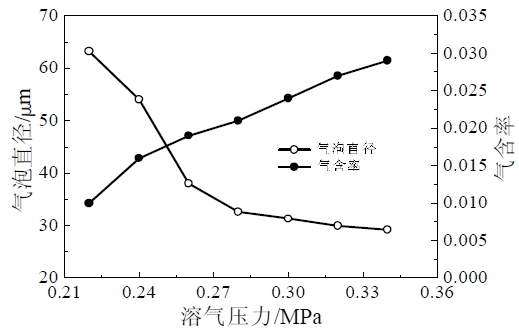
图2 溶气压力对气泡直径及气含率的影响
根据气含率和气泡直径可求得回流水中气泡数密度(即单位体积水中微气泡个数),研究可知气泡数密度随溶气压力升高而增大。油滴的数密度一定时,油滴分离率与气泡数密度成正比。提高溶气压力改善浮选效果的原因在于其增大了气泡的数密度。
2.2 化学助剂的影响
2.2.1 絮凝剂的影响
不同浓度聚合氯化铝(PAC,分析纯)对除油率变化的影响如图3所示。加入30mg/L聚合氯化铝,除油率明显提高,PAC投加量增大至60mg/L时,最终除油率达到98%以上,继续增大PAC投加量无法进一步提高除油效率。
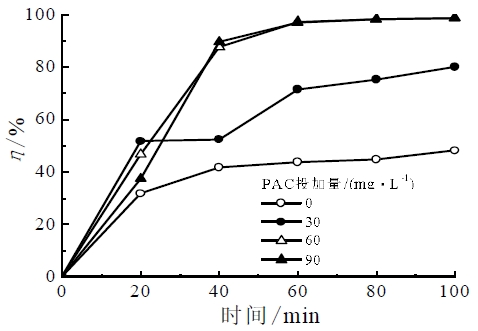
图3 聚合氯化铝浓度对除油效率的影响
观察PAC前后乳化油的显微图像可知,加入PAC后,油滴聚集成团簇。团簇相对单个油滴体积更大,更容易捕获微气泡,且粘附的气泡数目增多,形成体积更大、平均密度更小的絮团。同时,油滴聚集过程中形成了直径更大的油滴。以上2种因素强化了浮选除油效果。
除分离效率这一指标外,处理后污水即气浮出口污水的含油浓度同样重要。出水含油浓度会对后续水处理流程产生显著影响,所以出水含油浓度常作为气浮单元的考察和控制指标。PAC投加量对处理后污水含油浓度的影响见表1。由表1可知,随着PAC的提高,出水含油质量浓度先降低后保持不变。特别是PAC投加量高于60mg/L后出水含油质量浓度降低至15mg/L左右,除油效果显著。
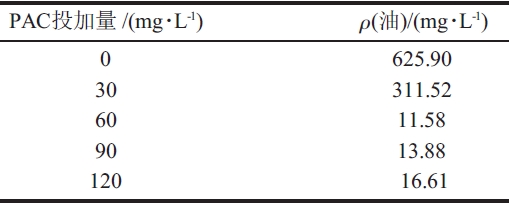
表1 PAC 投加量对处理后污水含油浓度的影响
考察了有机絮凝剂聚丙烯酰胺(PAM) 的作用。PAC和PAM对除油效率影响的对比见表2。实验用PAC和PAM投加量均为10mg/L,结果表明,PAM对浮选除油的改善效果有限,PAC能够更显著地改善除油效果。
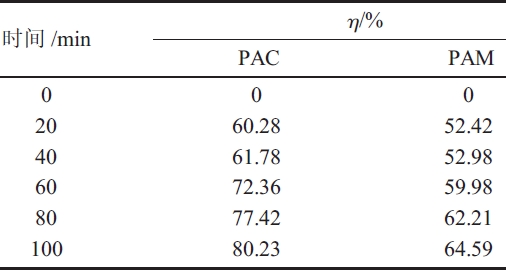
表2 PAC 和PAM 对除油效率的影响
2.2.2 表面活性剂的影响
不同表面活性剂十二烷基硫酸钠(SLS,分析纯)浓度下除油效率随时间的变化趋势见图4。由图4 可知,随SLS质量浓度由10mg/L增大至60mg/L,最终除油率由60%左右提高到90%以上。此后,除油效率不再随SLS浓度的增大而提高。
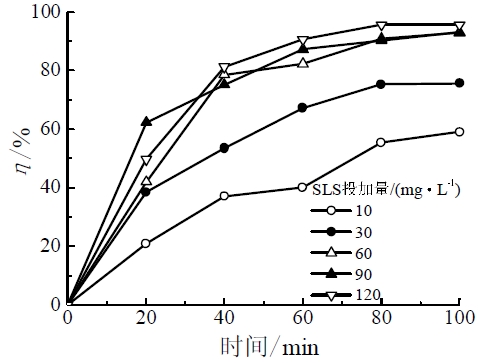
图4 十二烷基硫酸钠对除油效率的影响
表面活性剂可降低水的表面张力,减小生成气泡的直径并抑制气泡聚并,减小气泡直径,提高碰撞频率。除影响气泡直径外,SLS能够改变油水界面的性质,提高碰撞导致粘附的概率并降低絮团破碎的概率。
在工业应用中,有必要进行实验确定合理的表面活性剂加量。过高表面活性剂浓度不会改善浮选效果,但增加了操作成本。
为了对比絮凝剂与表面活性剂对浮选除油效果的影响,研究不同浓度聚合氯化铝和十二烷基硫酸钠对除油率的影响,结果如图5所示。由图5可知,当加药浓度为10mg/L 时,PAC对除油的改善效果明显优于SLS;加药浓度提高到30mg/L 时,PAC和SLS均能明显改善除油效果。所以PAC在加药浓度较低时即可改善除油效果,而表面活性剂则需要在浓度达到一定量时才会有较好的效果。
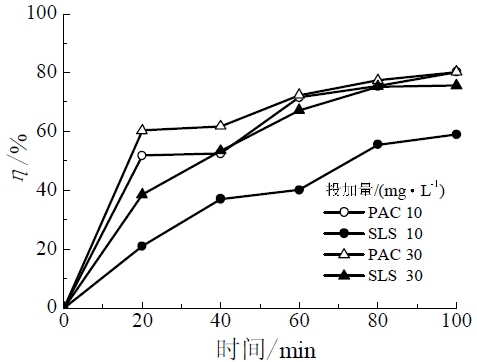
图5 PAC 与SLS 对除油效果的影响
3、结论
本文应用溶气气浮法处理乳化油污水,研究了溶气压力、处理量、表面活性剂及絮凝剂对除油效率的影响,结合浮选动力学模型对以上因素的影响机制进行了分析。研究表明,除油效率随溶气压力增大先提高后保持不变。溶气压力改善气浮除油效果的主要原因是其增大了污水中的气泡数密度。
无机絮凝剂聚合氯化铝可使油滴聚集成簇,提高气泡捕获概率,改善除油效果。有机絮凝剂聚丙烯酰胺则对除油效果的改善程度有限。
加入活性剂十二烷基硫酸钠可提高除油效率,达到一定值后继续增大表面活性剂浓度不会进一步提高除油效率。相较PAM 和SLS,PAC 可以在低浓度下更好地改善气浮除油效果。
友情提示:
您只要致电:021-60766769 (0)15216837090(张经理)
我们可以解答
气浮实验装置,
圆型气浮实验装置,
平流式加压气浮实验设备相关疑问!
我们可以帮您推荐符合您要求的
气浮实验装置,
圆型气浮实验装置,
平流式加压气浮实验设备相关产品!