表面贴装技术在电子工艺实习中的运用研究
伴随表面贴装技术的发展、推广,我国已然转变成全球第一表面贴装技术产业大国。对于当代大学生而言,掌握表面贴装技术工艺知识原理显得尤为关键。将表面贴装技术运用至电子工艺实习中, 要求学生自己动手操作, 如此一方面可促进学生了解掌握新技术、新工艺,一方面可促进学生了解认识为电子产品应用该项技术的发展形势,对于我国高等教育实际工程训练、国家经济发展也十分有必要。由此可见,对表面贴装技术在电子工艺实习中的运用开展研究,有着十分重要的现实意义。
1 表面贴装技术及其特征
1.1 表面贴装技术
表面贴装技术(Surface Mount Technology,SMT),是指把贴片元器件(SMC)贴至印刷电路板(PCB)上的一项新型电子产品装配技术,具体而言即为借助工具于SMB 板焊盘处涂上焊膏印或者粘接剂,然后把SMC 引脚与焊盘相连,最后选用回流焊或者波峰焊等手段开展焊接,进一步实现电气与机械之间的连接,表面贴装技术如图1 所示。
作为一项系统复杂的工程,表面贴装技术涉及到表面安装元器件技术、SMT 组装设计技术、SMT 设备技术、SMT 工艺制造技术、SMT 基板制造技术等多门学科、技术。和传统通孔技术相比较,表面贴装技术可以元器件作为主要区分,通孔技术所采用的为长引脚元器件,元器件以插入焊盘孔内的组装方式置于印刷电路板上;而表面贴装技术所采用的为短引线或者无引线元器件,且元器件以贴装在印刷电路板表面的组装方式置于印刷电路板上。此外,在焊接方式上,两项技术同样存在一定差异,表面贴装技术推行回流焊接法或者波峰焊接法,通孔技术则推行焊料熔化焊接法。
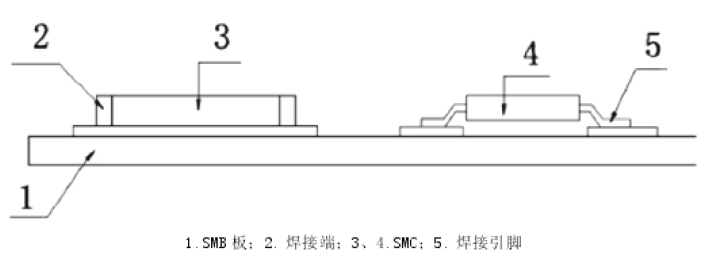
图1 表面贴装技术示意图
1.2 表面贴装技术特征
SMT 表面贴装技术特征,具体而言:(1)组装体积小、密度高,和通孔元器件相比较,表面贴装技术所采用的贴片元器件体积明显减小,重量也仅为通孔元器件重量约10.0%。相关研究指出,应用表面贴装技术后,电子产品体积可减少40.0%~60.0%,重量可降低60.0%~80.0%。(2)较强的可靠性,凭借贴片元器件体积较小、重量较轻及焊点缺陷率较低,因此表面贴装技术具备较强的可靠性,并且抗震能力同样得到一定改善。(3)良好的高频特性,表面贴装技术采用的为短引线或者无引线元器件,由此极大水平降低了寄生电感、寄生电容存在的可能,进一步强化了电路高频特性,消除了电磁、频射引发的干扰。
(4)低成本,因为贴片元器件体积减小,所以印刷电路板使用面积同样会得到一定降低,相继电子产品体积也得到减小,由此极大水平缩减了电子产品的生产成本;印刷电路板无需大量的钻孔,由此可显著降低电子产品维修成本;此外凭借SMT 良好的高频特性,有效降低了电子产品电路调试成本。相关研究显示,应用表面贴装技术后,电子产品生产成本降低了30.0%~50.0%,极大程度缩减了人力、物力等方面的损耗。
2 表面贴装技术在电子工艺实习中的运用
2.1 表面贴装技术组装种类及流程
表面贴装技术牵涉到多个不同专业及学科技术, 在涵盖其设备本身关联技术包括SMC 封装制造、电路布局、电路基板、焊接等的同时,还涉及检测、清晰、维修等相关技术。表面贴装技术组装种类可按照元器件、组装方式开展划分,分别有全表面组装、单面混合组装以及双面混合组装。其中,全表面组装指的是PCB 单面或者双面所选取元器件都采用贴片式元器件组装方式。这一组装种类具备操作简便、元器件体积小、质量轻等特点,对应工艺流程为:锡膏印刷→检测→贴装元件→检测→回流焊接→检测。
单面混合组装指的是PCB 单面所选取元器件采用贴片元器件与通孔元器件相混合的组装方式。该种组装种类有着较为复杂的工艺,不过由于其存在一些元器件为通孔封装式,有时同样要应用到通孔元器件,因此该种表面贴装技术组装种类同样较为适用。对应工艺流程为:锡膏印刷→检测→贴装元件→检测→回流焊接→检测→插件安装→检测→波峰焊接→检测→冷却→清洗→检测。
双面混合组装涵盖有两类情况,一类是PCB 一面均选取插装法开展通孔元器件安装,另一面均选取表面贴装法开展贴片元器件安装; 一类是PCB 双面所选取元器件同时有通孔元器件和贴片元器件,通孔元器件焊接于元器件背面上,贴片元器件焊接于元器件同面上。双面混合组装对操作人员工艺水平提出了较为严苛的要求,同时焊接不可一次性完成,在安装另一面元器件过程中,要求将之前插装好的元器件开展加固后方可开展。对应工艺流程为:锡膏印刷→检测→贴装元件→检测→回流焊接→检测→插件安装→检测→波峰焊接→检测→冷却→清洗→检测。
表面贴装技术三种不同组装种类均有着各自一定的优势, 工艺流程复杂水平同样存在一定差异,在电子工艺实习中,教师可结合电子产品具体装配要求选取适用的组装手段。
2.2 表面贴装技术实习教学流程
表面贴装技术实习教学流程,具体而言:(1)实习指导教师向学生讲授电子装配技术发展历史、趋向,使学生对电子组装主流工艺技术形成一定认识,扩宽学生学习视野,调动起学生电子工艺学习主观能动性。(2)实习指导教师向学生讲解SMT 相关电子产品工作原理。(3)实习指导教师向学生介绍SMT 工艺流程,学生结合SMT 工艺流程开展SMT 相关电子产品装配及相关插装元件焊接。(4)实习指导教师向学生讲解验证、调试技巧方法等。学生结合要求对SMT 相关电子产品进行验证、调试。(5)教师与学生开展全面探讨,教师、学生相互间就学生制作电子产品开展评价。
2.3 表面贴装技术教学工艺流程
表面贴装技术教学工艺流程包括: 来料检测→锡膏印刷→贴装元件→贴装质量检测→回流焊接→清洗→检测→返修,全面教学工艺流程需要运用到手动锡膏印刷台、焊膏专用冰箱、手动贴片台、激光钢模板、回流焊机以及真空吸笔,以上关键教学工艺流程包括锡膏印刷、贴装元件和回流焊接。(1)锡膏印刷。选取手动锡膏印刷台,采取刮刀把锡膏经由激光钢模板漏印至PCB 焊盘处。全面丝印流程可划分成两步:第一步,锡膏搅拌,搅拌具备两方面作用,一方面是将锡膏搅拌均匀,一方面是调节锡膏粘度。印刷性能优劣受锡膏粘度很大程度影响,倘若锡膏粘度过低,则极易出现流淌、塌边情况,进而影响到线条平整性及印刷分辨率;倘若锡膏粘度过高,将提升锡膏穿过模板开孔难度,进而造成印出线条缺乏完整性。将锡膏存储于0℃~4℃环境下, 自焊膏专用冰箱取出锡膏置于温度控制在20℃~25℃范围, 相对湿度控制在40.0%~60.0%, 使锡膏自然升温约20min,后选取玻璃棒开展搅拌。第二步,丝印焊锡膏,选取一定厚度的激光钢模板,选取手动锡膏印刷台,采取刮刀把锡膏经由激光钢模板漏印至PCB 焊盘处,以为元器件焊接提供准备。丝印焊锡膏是表面贴装技术教学工艺流程的首道工序,还是表面贴装技术质量的重要前提。选取刮刀漏印模板印刷手段对焊锡膏开展涂覆。在印刷过程中,利用刮刀通过相应速度、压力对焊锡膏进行推动,有效保证焊锡膏经由激光钢模板上焊盘漏孔分配至PCB 焊盘处。相关实践得出,焊接质量完备,焊盘锡量饱满,同时不出现桥接情况。(2)贴装元件。贴装元件指的是借助贴片机将表面贴装元器件有序安装至PCB对应焊盘位置处。在开展印刷板生产前,均要借助贴片机对印刷板开展编程,编程过程中应当结合元器件封装形式差异及送料器所处位置差异等开展编写,编程结束后,依托这一印刷板开展元器件贴装过程中同样务必要结合程序进行,所以务必要确保编程操作的准确性,有效防止由于病程不当而造成印刷板不可使用,在元器件贴装过程中必须要对首板开展检测。在对印刷板开展编程过程中,应当坚持结构简单到结构复杂原则,也就是先编写阻容类元件程序,后编写芯片类元件程序,每一步编程操作结束后均要予以封装,各个元件程序编写结束后系统会自动进入下一元件的编写。值得一提的是,如果元件具备方向性,那便需要结合图纸对应注明依据正确方向开展放置。除此之外,在焊接芯片类元件前,务必要全面检测引脚,确保其平整、完好。编程完毕后即可开展贴片操作,该环节由贴片机按照编写好的程序开展自动化操作。在实际实习中,通常选取的设备为手动设备而并非工厂生产线先进的自动化设备,因此在贴装元件流程中要推行手工贴装,元件手工贴装指的是选取真空吸笔把表面贴装器件有序安装至PCB 对应位置上。贴装静电敏感器件务必佩戴防静电腕带,并于接地可靠的防静电工作台上开展贴装;务必要依据装配图要求开展贴装方向选取;贴装位置准确,引脚、焊盘相对齐;元件贴防后要借助镊子缓缓锨压元件顶部,确保贴装元件引脚超过一半厚度浸入焊膏中。(3)回流焊接。元件贴片结束后应当开展检测,通过检测确保不存在误贴、方向、错误等情况后将印刷板置于回流焊炉传送带处, 进入最后一项表面贴装技术教学工艺流程———回流焊接。就回流焊接而言,首要工作是开展好温度控制。回流焊接可划分成预热、保温、回流及冷却四个步骤。其中,预热指的是对PCB 进行加热, 将PCB 由室温升高到150℃~170℃, 进一步迅速转至保温过程;保温是为了确保元器件能够维持在一个较为稳定的温度状态,从而缩减每一元器件相互间的温差,进一步实现电路板稳定平衡,通常保温区稳定调节在约180℃。于回流区开展加热过程中,加热器稳定调节要低于245℃, 以确保每一元器件稳定可迅速升高并实现最高值。加热结束后,通过传送带把PCB 板送出炉膛,并将其置于室温下自然冷却。在加热期间,焊膏中锡粉末实现熔化、湿润,于此期间焊膏可与PCB 板表面相连, 通过一定时间自然冷却后,PCB 板就会呈现出明亮、有序的焊点。在开展回流焊接过程中,环境适度极大程度影响着回流焊接质量,如果环境适度超过75.0%,零件引脚、金属部位便极易形成白色腐蚀物,所以在操作实践中,必须将环境湿度调节在40.0%~60.0%范围,从而为回流焊接质量提供有效保障。
表面贴装技术实习产品为收音机制作,收音机制作流程,如图2所示。其中,以手工贴片为流程首要难点。因为贴片元件体积小,再加上各个规格、型号元件外观大致相同,尤其是对于贴片电容,规格参数未有标记,所以贴片过程中时常会发生差错。学生自工位1 于印好焊膏印刷板处,选取真空吸笔对元件1 进行贴装,在转至工位2 对元件2 进行贴装,以此类推,实现对所有贴片元件的贴装。通过一系列实践得出,该种组装方式开展有序、适应性佳、成功率高。
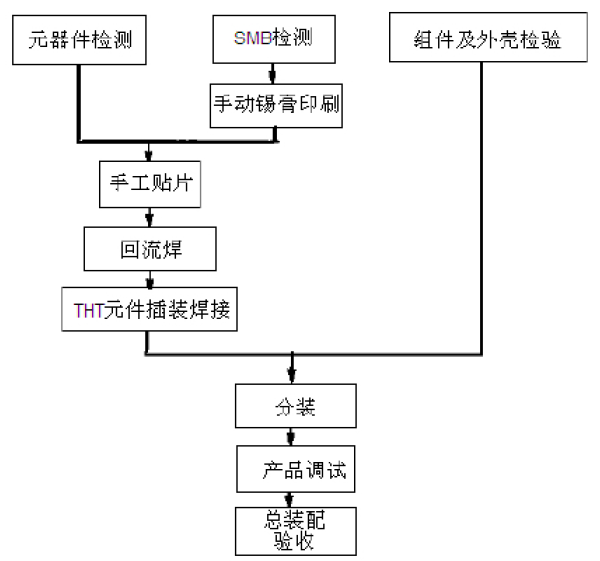
图2 表面贴装技术产品制作流程示意图
3 表面贴装技术教学效果
表面贴装技术在电子工艺实习中的实践运用, 得到了学生的一致认可,并收获了可观的教学成效,学生们经由自己动手对表面贴装技术全面工艺流程开展实践操作,加深了对SMT 设备器件爱你的认识,掌握了SMT 工艺,强化了自身实践能力、实际问题解决嗯呢管理。学生们一致认为,表面贴装技术在电子工艺实习中的实践运用,自己动手制作电子产品,收获了十足成就感,改善了电子工艺实习效果。
结束语
总而言之, 电子工艺实习是高校培养学生实践能力的有效途径之一。在强化实践能力培养的同时,要求把培养综合性高素质人才的理念引入实习教学中,所以在电子工艺实习过程中引入新的教学内容仅为关键。相关人员务必要清楚认识表面贴装技术及其特征,强化表面贴装技术在电子工艺实习中的科学合理运用,不断钻研研究、总结经验,积极促进电子工艺实习有序开展。