PLC控制混合机液压系统的设计与实现
混合机是中国工程物理研究院化工材料研究所的重要设备,主要用于一定温度和一定真空度下几种物料的混合。设备主要包括主机、液压系统、真空系统、气动系统、热水系统及控制系统等部分,是典型的机电液自动化设备。其中,液压系统是设备的最重要组成部分,液压系统是主机升降和混合桨旋转的动力源。该设备购置于20世纪90年代末,由于液压、控制系统的技术局限和元器件老化,造成设备性能下降、精度下降等问题,近期出现升降和旋转动作异常现象。针对以上问题和现象,需重新设计液压控制系统,而主机、气动和热水系统利旧,达到既能保证科研生产的需要又节约成本,最大限度地利用设备的目的。
1、液压控制系统的功能要求
混合机液压系统的升降和旋转要求动作平滑、控制平稳、精度在±2r/min。系统实现的功能如下:
a.调节旋转方向和无级调速。
b.要求能够实现远程控制(以下简称远控)和就地控制(以下简称近控)两种功能。远控在控制大厅的控制台计算机上进行操作,近控在主机现场操作。
c.手动和自动两种控制方式。手动工况下,按照需求实现升降、旋转等单步动作; 自动工况下,在温度、真空度等其他条件达到后,实现主机和混合桨自动按设定位置、设定升降、设定时间、设定工段、设定转向和设定速度进行升降、旋转等全工艺过程动作。
2、硬件部分
混合机液压控制系统的硬件设计以PLC系统和计算机系统为核心,计算机与PLC的CPU之间通过通信电缆实现双向数字通信。
PLC是一种专为在工业环境中应用而设计的具有计算机功能的电子装置。可执行逻辑运算、顺序运算、定时、计数及算术运算等操作指令,通过数字式、模拟式的输入输出使外围设备与工业控制系统形成一个整体,实现对各类机械或生产过程的控制。PLC机型选择的基本原则应该是在满足功能要求的情况下,主要考虑结构、功能、统一性及在线编程要求等。本系统采用三菱FX3U,包括CPU模块、AD模块和DA模块。PLC收集行程开关、按钮等开关量信号,温度、压力等传感器模拟量信号; CPU进行信号处理、数学运算等程序处理,发出指令驱动液压系统的升降油泵、旋转油泵、升降阀及旋转阀等按程序完成动作。
输入输出单元是PLC与外界连接的接口。输入单元接收来自用户的各种控制信号,通过连接电路将这些信号转换成中央处理器能够识别和处理的信号。CPU读取输入信号并进行处理,然后将处理结果输送到输出单元,输出单元控制设备的执行元件。
混合机液压控制系统的硬件配置如图1所示。根据系统的工艺要求、控制功能和I/O点数选择的三菱FX3U,其CPU模块为FX3U-128,包含128点DI(开关量输入模块) 、DO(开关量输出模块),扩展模块为两块3U-4AD(4通道模拟量/数字量转换模块)和一块3U-4DA(4通道数字量/模拟量转换模块)。行程开关、按钮、旋钮及超温超压超速报警信号等作为开关量输入至CPU模块,CPU模块输出开关量控制信号至油泵、真空泵及空压机等接触器和中间继电器,上升阀/下降阀/正转阀/反转阀等,位置、升降、旋转等状态指示灯。4AD模块用于油温、料温、夹套温度、真空、转速及油压等传感器模拟量的运算处理。4DA模块用于转速比例放大。
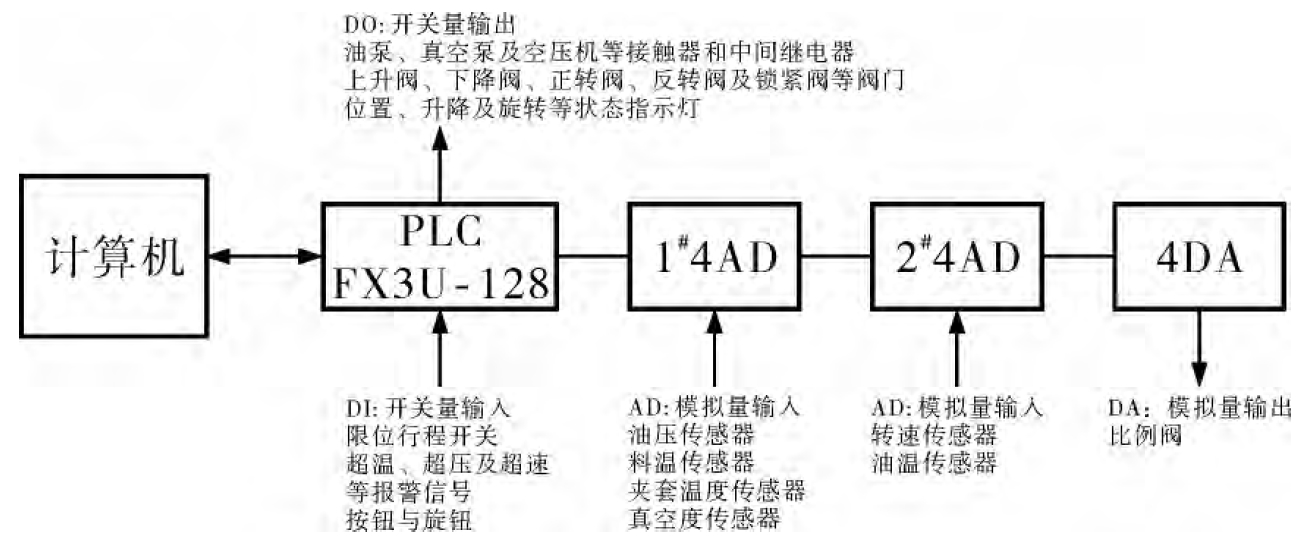
图1 混合机液压控制系统的硬件配置框图
利用电液比例控制技术实现液体压力和流量连续且按比例地跟随控制信号而变化。电液比例阀的优点有: 方便地实现自动控制、远程控制和程序控制; 把电的快速性、灵活性等与液压传动功率大等优点结合起来; 连续且按比例地控制执行元件的力、速度和方向,并防止压力或速度变化时的冲击现象。组成电液比例控制系统的基本元件包括:
a.指令元件,产生并输入给定控制信号;
b.比较元件,把给定输入与反馈信号进行比较,得到的偏差信号作为电控器的输入;
c.电控器,对输入信号进行加工、整形和放大,以便达到电- 机械转换装置的控制要求;
d.比例阀,电、机械转换器和液压放大元件。
混合机的旋转控制采用了比例放大技术,由比例阀和比例放大器实现。通过电信号大小控制比例阀的换向与开度,从而控制混合机的旋转换向和速度控制。本系统采用的比例放大器包括电源、信号源输入、信号处理及比例放大板等,它与比例阀配套使用,设有整流、滤波、稳压、过载保护、信号输入、斜坡升降调节、前置放大及功率放大等有关电路。
转速比例放大原理框图如图2所示。控制转速有手动、自动两种模式。手动方式由人工调节电位器,输入信号至比例放大器,比例放大器相应输出0~680mA信号至比例电磁铁,驱动比例线圈,实现油口切换和不同开度的目的,达到混合桨旋转方向和不同速度的要求; 自动方式从计算机上设置转速,PLC程序进行转速显示、控制、运算和信号处理,得到转速控制信号,转速控制信号通过4DA模块将数字信号转换为模拟量信号1~5V(DC),该信号输入至比例放大器,比例放大器相应输出0~680mA信号至比例电磁铁,驱动比例线圈。
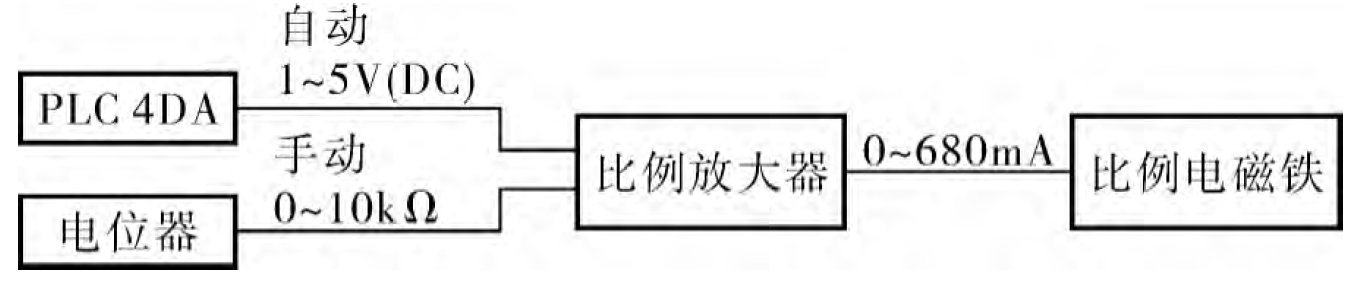
图2 转速比例放大原理框图
3、软件部分
3.1转速自动控制程序
计算机操作软件采用组态王6.55软件,实现全工艺过程的显示与操作,包括参数显示、状态指示、工艺设定及主机操作等。
混合机液压控制系统的转速自动控制程序由PLC实现,开发平台为三菱GX Developer。转速自动控制流程如图3所示。
检查DA模块是否正常,与机架号比较,若出现错误则进行报警处理。然后定义DA模块量程,即4个通道都为-10~10V(DC)输入,相应为-10000~10000个字。当执行自动程序时,首
先判断是否满足自动条件,即是否有液压油堵、超温、超压和主机位置不到位。如果有,则进入报警程序处理; 如因意外情况导致转速超速,则进入限速和报警处理程序。实际转速与设定转速比较,设置判断带宽,如果实际转速小于设定值带,则增加DA模块的输出量,直至等于设定值为止。如果实际转速大于设定值带,则减小DA模块的输出量,直至等于设定值。带宽不能过大,否则转速控制不平稳,精度不够; 带宽也不能过小,否则执行机构频繁动作,影响性能。经多次调试,比例放大系统和转速自动控制系统的各个参数都达到了要求,系统动作平稳,控制精度优于工艺要求。
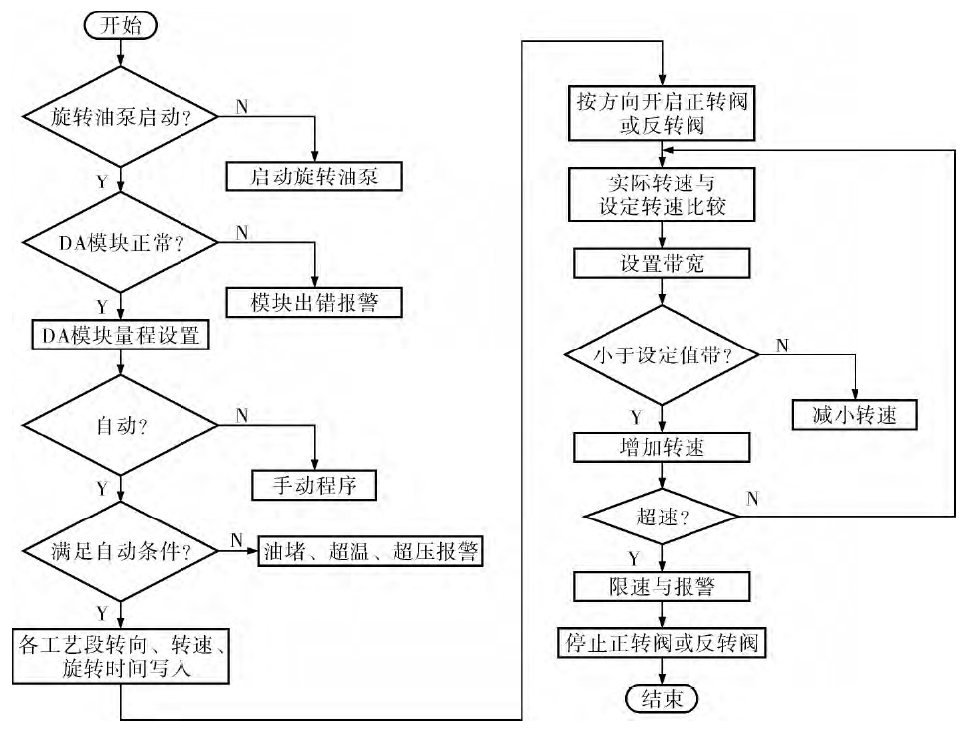
图3 转速自动控制流程
3.2转速测量参数及其调试
转速传感器输出脉冲信号至控制系统,转速V 的计算公式如下:

式中f ———频率输入值,Hz;
KK1———输入增益;
KK2———传感器每转发生的脉冲个数;
KK4———标度增益;
PB1———输入零点;
PB4———标度零点;
SL0———转速时间,min。
计算由CPU完成,SL0、KK2、KK4和PB4用于标度转换,KK1和PB1用于精度调整。在本系统中,液压马达每转一圈,传感器感应10个脉冲。
经多次调试后确定了相关参数,测试结果表明其测量线性度好,测量精度优于工艺要求。本系统中转速V与频率f的关系曲线如图4所示。
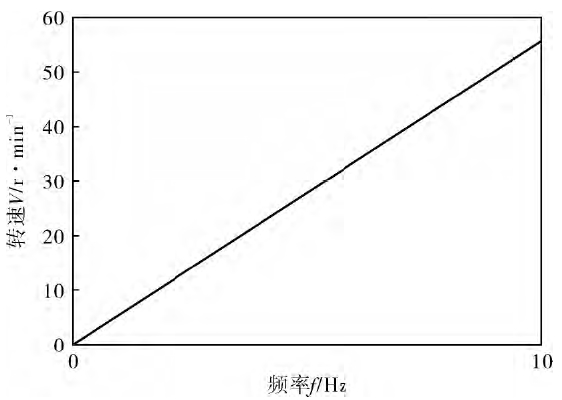
图4 转速与频率的关系曲线
3.3安全设计
由于混合机混合的原材料属危险品,属危险作业,因此,为保证生产过程、设备和操作人员的安全,安全系统设计非常重要。
3.3.1转速安全保护
转速安全保护设置两级转速保护,由PLC程序实现。其中,二级为设定转速的110% ,一级为图4转速与频率的关系曲线设定转速的120%。
在正常情况下,当转速达到设定转速时,PLC会自动停止增速。当有意外发生,如果没有停止增速,且转速升高到二级指标时,PLC发出控制信号实施速度钳位,并发出声光报警。如果转速失控,仍然升高,当转速升高到一级指标时,PLC发出控制信号,立即停止转动,并开始卸真空和主机下降,直到达到下限位,同时发出声光报警。
3.3.2安全联锁
为实现安全联锁,设计远控系统用于在控制大厅进行远程隔离操作,从操作上保证了安全。
PLC程序中设计的安全联锁有:
a.远控/近控联锁,处于远控状态时,近控所有操作无效; 反之,处于近控状态时,远控所有操作无效。
b.正转/反转联锁,处于正转状态时,反转操作无效; 反之,处于反转状态时,正转操作无效。
c.门机联锁,设备处于运行状态时,启动开门无效; 如果没有关好门,启动设备无效。
d.手动/自动联锁,处于手动状态时,自动操作无效; 反之,处于自动状态时,手动操作无效。
3.3.3超限处理与报警
超限处理与报警由PLC 程序实现,触发源与报警处理详见表1。
触发源超限 |
处理与报警 |
主机超温 |
停止转动,主机下降,声光报警 |
夹套温度 |
超温停止加热,声光报警 |
油温超温 |
油加热器停止,声光报警 |
漏油 |
主机下降,油泵停止,声光报警 |
扭矩超限 |
主机下降,油泵停止,声光报警 |
主机未到位 |
不能进行上升操作 |
超压 |
油泵停止,声光报警 |
超速 |
停止转动,声光报警 |
表1 超限处理与报警项目
3.3.4急停
当有意外情况发生时,按下“急停”按钮,停止油泵、升降、旋转、加热及抽真空等全部的动力动作,以保证工作人员、生产和设备的安全。
4、结束语
混合机液压控制系统采用PLC、电液比例放大控制等技术,实现液压系统的主机升降和旋转的各项功能。采用了安全保护、安全联锁等设计,保证生产过程和工作人员的安全。实际运行表明: 该控制系统具有功能完善、性能可靠、操作方便、易于网络化管理及易于设备扩充等特点,具有一定的先进性和推广性。